A greener ramp?
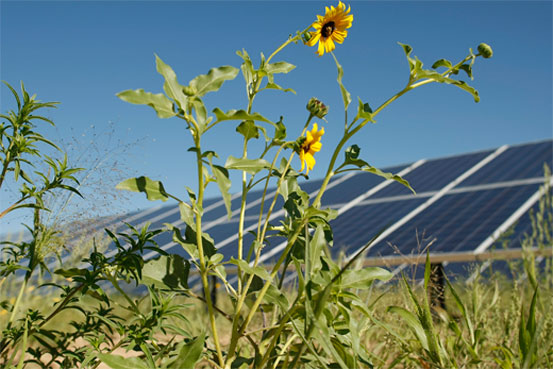
In an ideal world, aviation stakeholders are all working hard towards a greener future. But just how quickly is that dream being realised?
Most readers are aware that the so-called green movement has its roots in the West Coast where, for many years, pollution has been a daily problem. It’s no surprise to learn, then, that in this area more than mere lip service has been paid to the concept of cleaner air. Progress has been steady and much has been written about the initiatives and developments that have occurred to improve the quality of life within the region.
However, such progress is reliant on many factors. For certain, airlines and handlers have been pushing for change, but what about the airports themselves? Do they have much of a contribution to make to the overall scene? And can they call the shots, if required? In this feature we talk to them, as well as the other stakeholders, to try and gain an overview of the status quo.
The funding factor
According to Roger Hooson, Senior Planner, Landside Operations at San Francisco airport, a lack of funding in recent years has slowed down the pace of the green movement somewhat. But, arrested though it has been, the process is continuing.
“Ramp equipment decisions are down to airlines and handlers,” he admits, “and this tends to be the situation at most airports. At San Francisco, we have a clean vehicle policy in operation although there are no specific mandates when it comes to airside operations. In this area, it is rather a voluntary decision. Diesel power is, of course, a factor in California and there has been a big move towards cleaner, alternative power.”
A question of quality At San Diego, it is a slightly different story.
“Airports have started to go green but mostly it has been the carriers that have led the way,” declares Brett Caldwell, Airport Planner at San Diego airport. That said, the airport authority conducts an annual inventory of all ground support equipment, which is part of the station’s overall Air Quality Management Plan. Brett takes up the story.
“The Air Quality Management Plan identified and evaluated specific aircraft ground movement emission reduction measures. Some of those measures included assessing aircraft taxi-in and taxi-out times, single-engine taxi-ing procedures and other ground-based greenhouse gas emission reduction measures.
“In addition, Southwest Airline gates at San Diego all have 400 hertz at-gate power and pre-conditioned air units. The airport is also installing 400 hertz at-gate power and pre-conditioned air at an additional 19 gates. Having these power and pre-conditioned air units reduces the air emissions associated with aircraft parked at the gates.
“Approximately 13.5% of the fleet here. which entails some 71 units of GSE, is electric. There is also an extensive system of GSE electric charging infrastructure in place. We also have about 17% of our GSE powered by alternative fuel: that’s just over 90 items of equipment.”
He adds that San Diego International currently has 41 gates, a figure that is set to increase to 51 gates by the summer of 2013.The airport will also be trying to acquire additional funding for projects to reduce the air emissions associated with its ramp operations. It’s worth noting, too, in this context that both the airport and its airlines do have recycling policies. In fact, the airport authority has won the City of San Diego Recycler of the Year Award for the last six consecutive years: that would be overwhelming proof of its ongoing commitment to the environment.
“The airport authority has a Green House Gas Memorandum of Understanding with the California Attorney General to reduce its greenhouse gas emissions. The commitments in the memorandum specifically address emissions reduction measures for airside activity, including the ramp, as well as landside ground transportation activity.”
Breath of fresh air at Seattle
Sea-Tac’s work in the environmental area really got a fillip in 2010: that was the year when the airport authority received some US$18.3m from the Federal Aviation Administration for a project expected to reduce greenhouse gas emissions. The Voluntary Airport Low Emissions grant was aimed at funding the construction of a pre-conditioned air project that would make Sea-Tac one of the nation’s few airports with a centralized system, one that covered the entire airport.
It was a landmark moment and scientists had calculated that such an initiative would cut down on CO2 emissions by up to 50,000 tonnes a year. In addition, airlines were expected to save up to 5m gallons of fuel annually, which equated to some US$10m a year.
Aircraft on stand would have the facility for hooking up to the pre-conditioned air units on the gates. Their usage allowed aircraft to dispense with auxiliary power units, the use of which generates pollutants; moreover, the aircraft would not expend fuel on running their on systems. To get the cool air aboard, piping was introduced – and an estimated ten miles of piping was to be used to complete the project.
In all, the cost of the entire project was estimated to be just over US$33m. Of this sum, the US$18.3m grant was to cover the first phase of the project that would encompass 53 of Sea-Tac’s 81 gates. The remaining cost was to be paid through Airport Development Funds, which would come directly from fees charged to airlines. Indeed, the carriers have been a useful driving force in this initiative. It was calculated that these fees would be more than offset by decreased airline operating costs that were put at US$10m per year for airlines at Sea-Tac. Although the end of 2011 was set as the target date for the completion of phase one, that date has since moved to the autumn of 2012, with the entire project due to be completed by the end of this year.
According to the airport’s spokesman, this is no small undertaking.
“The size of this project is unusual for an airport in a temperate climate like ours, but we’ve shown this can make a tremendous impact on our environmental footprint, one of our key goals,” says Mark Reis, Sea-Tac Airport’s Managing Director. “The positive effects also include reduced noise from aircraft while they are parked at the gates.”
Overall, the project’s main objectives were to decrease the amount of energy used to heat and cool the aircraft and shift the energy demand from fossil fuels to low carbon, electrical sources. Less CO2, minimized life-cycle costs, lower fuel consumption and less noise on the ramp were all useful gains to be found within the framework of the exercise.
The first phase of the PC Air project has seen the construction of the Central Plant, portions of the Chilled and Heated Water Distribution System, the purchase of the gate delivery equipment and installation of the gate delivery equipment at approximately 50 of the 73 gates.
Another project getting underway relates to the use of electric GSE. Currently being put together is a pilot project for chargers on the ramp that is expected to spread to all areas. This is scheduled to be up and running in October.
The airport has a 25 year plan when it comes to environmental matters. Since 2005, for example, it has been using underground hydrants to transfer fuel to passenger gates, obviating the requirement for bowsers, which obviously cause pollution. Annually, this measure has reduced levels of CO2 by 42,000 pounds a year whilst 64,000 pounds of nitrous oxides have been saved.
In October 2011, the Port of Seattle Commission adopted a number of policies, all of which were aimed at pushing Sea-Tac to the forefront of US ports for environmental stewardship and energy efficiency. Measures mooted included reducing air pollutant emissions by 50% compared to 2005 levels; reducing aircraft-related greenhouse gas emissions by 25%; and cutting carbon emissions by 50%, based on 2005 data.
Let it snow…
Denver airport’s background is an enviable one in terms of sustainability and environmental concern. In fact, the airport’s environmental management has chalked up many accolades over the last few years, both in the US and on the international stage.
In 2004 it was accepted into Colorado’s environmental leadership program as a Gold level member. It was also, inter alia, the first airport in the US to join the EPA’s National Environmental Performance Track Program: that was back in 2006. A year later it received the FAA’s Environmental Stewardship Award. Today, the airport recycles or reuses 21 different types of materials, including around 71% of collected aircraft de-icing fluids, something that should be elaborated on here.
The fifth busiest station within the US is known for its winter ski-ing season which of course infers that there is plenty of snowfall – and because of this fact, de-icing procedures are an important element of ramp activity during the winter months. Whilst airlines and handlers take responsibility for much of the green movements on the ramp, nonetheless the airport authority has its say when talk turns to safe operation and keeping the environment clean.
Much, but not all, of the de-icing takes place at remote pads at the airport and the authority has seen fit to introduce various rules about moving aircraft safely off stand to these remote pads. An initial spray at the gate entails the employment of Type 1 undiluted fluid, which is restricted to 25 gallons in total per application. A simple trench system around the gates ensures the spent fluid is collected but because it’s a large area, so the fluid becomes very diluted. Where the glycol content falls below 1% it is not worth (in economic terms, at least) recycling.
Interestingly, Great Lakes turbo-props are de-iced on the stands rather than out on the pads. Because these regional jets are small, it’s deemed better to treat them separately: in that way, the bigger carriers experience no hold ups on the remote pads. Great Lakes has a busy schedule at Denver and so the fleet’s run-off accumulates in an average day. An underground pan catches the spent fluid and this can be considered a customised solution for the carrier.
Nevertheless, Denver airport runs an efficient glycol recycling operation, which dates back a couple of decades. This was vastly upgraded in 2004, thanks to a new contract that saw the introduction of mechanical vapour recompression units, amongst other features, which have since more effectively addressed the separation of glycol from waste water.
But what about those remote pads? Having a dedicated area (or in this case, areas) means that with the huge volume of traffic that passes daily in the winter months there is a proportionately large quantity of spent glycol to recover. In all, about 71% of its used glycol is reclaimed and recycled. When the strategy got underway back in 2004, that season saw 306,785 gallons recouped. Since then, around 558,000 gallons has been the annual average, which equates close to US$3m in terms of value.
Greenprint Denver, the City’s Sustainability Initiative, includes a goal of 69% total collected of applied aircraft de-icing fluid. The percent collected comprises three components, namely volume of glycol reclaimed, volume of glycol sent to the wastewater treatment plant, and the volume of glycol waste sent to landfill. The airport has met or exceeded the 69% goal for the past eight years and the spokesperson says that it is always striving to increase its collection efficiency for both environmental and economic reasons.
However, it’s not all about de-icing. Keith Pass, the airport’s Environmental Program Administrator, says that the authority encourages the adoption of greener GSE, too. Compressed natural gas is used extensively around the site and indeed, Denver’s fleet of CNG-powered vehicles is amongst the largest that you’ll find in the country. Currently there are in excess of 300 vehicles that rely on alternatives to diesel: a good number of these (over 100) are battery powered whilst some are running on a combination of battery and hybrid power. Helping the electric side of the equation has been ongoing work on solar panel arrays: Denver International currently has no fewer than three solar array systems that produce approximately 6% of the airport’s total power requirements. Such output makes the airport the largest distributed generation photovoltaic energy producer in the state of Colorado. Whilst bio-diesel has also been trialled here it was found that performance was impaired by the very cold weather that can be a feature of this particular station.
The greener GSE fleets are augmented every year and Keith notes that handlers are generally receptive to this ongoing change; handlers are also looking at other stations for materials and leads that could be useful to their operations at Denver.
The other big news at the station has been the installation of pre-conditioned air units on jetbridges, which has the positive effect of cutting down aircraft engine use whilst on stand: all stands are thus equipped, with commensurate benefits.
And the future?
“When the next runway is built,” concludes Keith, “we shall certainly incorporate a de-icing recovery system. Concourse expansion will also allow for pre-conditioned air. We are engaged on a sustainability master plan, so we are certainly looking ahead.”
Oakland: on a charge
According to Susan Fizzell, who is Environmental Planner at Oakland International airport, the authority is engaged in a number of initiatives to make the ramp more environmentally-friendly.
“We recently completed a project that provides 400Hz at all our gates, as well as remote parking locations that will reduce the amount of jet fuel burn at gates,” she reveals. “Pre-conditioned air is provided at most gates now and we are working to complete its installation on our remaining gates, again with a view to reducing jet and diesel fuel burn. Aside from this, we have installed bridge power managers that allow GSE to be charged from the bridge traction power supply when the bridge is not in use.
“Though the airport itself does not own any GSE, we have encouraged our tenants to convert to battery-powered GSE by providing the necessary electrical infrastructure.”
On a slightly different note, in April this year the airport hosted an AOA Spring Cleaning event which targeted the airfield and ramp areas. A staggering total of 20.4 tonnes of débris was collected, of which 18.6 tonnes was recycled. Similar events are due to be held on a semi-annual basis, with the next one planned for October this year.
Food for thought?
Massport: more electric GSE
At Massport, the situation is a little more complicated. According to Stewart Dalzell, who is Deputy Director Environmental Planning and Permitting, nearly all of the station’s ramp areas are managed by individual airlines and/or FBOs. As such, there would seem to be many different procedures in place and there is no one individual at Massport that directly manages these ramp practices.
“However,” he notes, “Massport has implemented some measures to improve ramp environmental performance. This would include 400 Hz power and/or pre-conditioned air at all 98 contact gates. There are a few that don’t have both right now, but we have a project to complete those locations. In addition, we are proceeding with adding GSE electrification rampside. Most notably, Massport recently provided a low-cost loan to Delta Air Lines to provide electric charge stations and to purchase 50 electric GSE: so we are slowly extending the GSE infrastructure as opportunities arise.”
Airlines: the key to the equation?
Whilst airports, as landlords, understandably take more than a passing interest in their environment, most of the time it is the airline that is prompting change for the better.
Southwest is just one example in this context, and it boasts an industry-leading electric ground support equipment program, which covers both conversion and new purchase.
Marilee McInnis, as spokeswoman for the carrier, says that Southwest has committed to entering new markets such as Charleston, Greenville-Spartanburg and Newark markets with new electric beltloaders and baggage tractors.
“With these new markets, we added 21 cleaner-burning units of GSE in 2011, yielding reductions in both fuel use and greenhouse gas emissions,” she confirms.
“Many of our original GSE have reached the end of their useful life, and in 2011, a large number of GSE were replaced with new, cleaner-burning diesel equipment. These new GSE, combined with the continuation of our GSE diesel-to-electric conversion program, brought the total number of cleaner-burning GSE in our fleet to more than 1,300 at the end of 2011.
“Using electric equipment in new markets is an opportunity to build a sustainable foundation from the beginning of our operations in new locations,” she adds, “and we will continue to fulfill our commitment to making environmentally responsible decisions with the use of cleaner-burning GSE.”
Modifying gates to provide power is another strategy that Southwest has embraced.
“Over the past few years, we have worked both internally and with airports to install gate electrification equipment. Now available in all cities where Southwest Airlines operates with bridge-based boarding, gate electrification allows our aircraft to be powered by electricity instead of jet fuel while parked at the gate: this represents a potential savings of more than 46,000 gallons of fuel in a single day. We continue our focus on immediate hookup, typically within 90 seconds of parking at the gate, to gate electrification equipment to maximize fuel savings.
With a 28 minute average turn time and a conservative estimate of six minutes to hookup and unhook gate electrification, this focus on immediate hookup can result in 22 minutes of avoided auxiliary power unit use, which in turn means a saving of approximately 15 gallons of fuel per event. However, gate electrification cannot be used in all circumstances, such as ground boarding, quick turnarounds, or in extremely windy conditions,” she concludes.
Beyond the Frontier
Frontier is also working to reduce its impact on the environment, specifically in terms of its airport operations.
When it comes to APU usage reduction, Frontier utilizes alternative terminal power systems or ground power units to reduce fuel consumption and emissions where possible. Recent efforts have focussed on reducing the time taken to power off an aircraft’s auxiliary power unit.
Single engine taxi–ing has been another feature, and this expedient has been followed for several years, where safe and feasible. In so doing, Frontier pilots have been taxi-ing using a single engine, cutting down on emissions and fuel consumption.
GSE materials recycling has been another measure: Frontier’s ground support maintenance facilities work hard to recycle any recyclable materials which are used to help power and run the carrier’s GSE. In 2011, approximately 33,000 pounds of metal and aluminum was recycled from Frontier’s Denver maintenance facility, for example.
Back in 2006, Frontier replaced all of its GSE pneumatic tires with webbed tires that not only last significantly longer than pneumatic tires, but are also made completely of rubber, making them 100% recyclable. And glycol recycling shouldn’t be omitted, either: in Denver, more than 70% of Frontier’s glycol fluid fused at the airport is recycled.
United effort
Meanwhile, United hasn’t been slow off the blocks.
Where possible, the carrier provides aircraft parked at the gate with air conditioning and electric power sourced through alternative, emissions-reducing methods. This is in place of an aircraft utilizing its own auxiliary power unit. As other carriers have noted, it’s a cost saving exercise: United reckons that an auxiliary power unit uses 40 to 100 or more gallons of fuel per hour, compared to terminal-sourced power or cooling systems or ground power units, which use, by comparison, under than five gallons per hour.
Wherever possible, the carrier also makes use of only one engine whilst taxi-ing
and it tries to ensure that GSE instead of aircraft engines is used to tow aircraft to and from and between gates.
Moreover, United’s interest in fuel economy extends well beyond its aircraft fleet: combined, United and Continental operate more than 3,600 alternatively-fueled (or zero-emission) ground service equipment vehicles.
In its Denver hub (which has already come in for a lot of environmental plaudits) United relies upon solar power to operate its fuel system. The fuel system relies on nine acres of solar panels which produce 1.6 megawatts of power. This application is sized to provide all the energy required for pumping fuel from the storage tanks to the waiting aircraft. Helpfully, during off-peak periods, United is able to sell power back to the grid, whilst at night and on overcast days, it buys power back from the grid.
All in all, it’s an illustration of just what can be achieved if a carrier has the necessary vision and determination.
Focussing on cleaner energy
From carriers to the raw materials. If you’re setting out to run a company, the main aim in life of which is to preach the gospel according to the environment, then Clean Energy would seem to be a highly apposite title for that entity.
This California-based enterprise is fully focussed on the ground side of the power equation, both on and off airport, although currently, the bulk of its work revolves around landside operations. Chad Lindholm is Vice President for the Western Region and he says that interest in the concept of alternative power, more precisely that of CNG, is growing year on year.
“There are several segments at an airport where we see the benefits. Taxi-cabs and shuttles are prime candidates; then there are courtesy buses, which can include rental transport, hotel cars and off-airport parking lots. Shared ride packages are also of interest.”
At the present time he underlines the fact that Clean Energy is not doing very much in connection with GSE. That’s not because there is no interest in CNG as a means of propulsion: the US is a rich source for this fuel and indeed, Chad notes that his company was behind the extensive infrastructure that enabled Denver airport to exploit this means of locomotion, as mentioned earlier in this feature. No, the overriding factor tends to be that of volumes used: in general, where GSE is involved, the relatively small quantities of CNG employed means that economies of scale are slower to be realized. “You need a significant amount of GSE to justify the adoption of CNG,” he says.
“Ultimately, the airport needs to be able to see a return on investment,” he explains. “Once that becomes visible, then things start moving. CNG has much to recommend it: it’s the cleanest fuel around, it’s readily available domestically, it’s abundant and there’s no greenhouse gases to worry about. If you’re using it correctly, in the right places, it can result in savings of up to US$2 a gallon at the pump.
“Today, we’ve brought this technology to 30 airports, so it’s no longer just a West Coast thing. At our older installations, Los Angeles and San Francisco, where we have 12 or 13 years’ experience, we’ve a 50% penetration, which means there is lots more potential. In fact, a second facility is due to be built at Los Angeles. These sites, plus Dallas Fort Worth, really showcase what we’ve been able to achieve.
“We’ve crossed the US with this technology: Las Vegas and Chicago are just two examples, and with new airports coming through, this technology has a rôle to play. After all, sustainability goals are being set by governments.
“In the earlier days, engines weren’t as technically advanced as they are now but all that has changed. We don’t necessarily advocate grants – in some respects, they are not needed, although funding is out there – since the return on investment is proven.
“As for the next few years, I am certain that our presence will continue to grow: we’ve a further 12 airports lined up for this technology.”
Bridging the gap
Finally, a word from JBT AeroTech, a specialist whose extensive GSE portfolio includes the design, manufacture and installation of jetways. In acknowledging the level of interest in the company’s airbridge products, Jim Cherrett, the company’s Marketing Manager Operations, points out that today, bridges are rarely ordered in isolation, but rather are supplied with pre-conditioned air and 400 Hertz power attached.
A sign of the times?