Rolling, rolling, rolling…
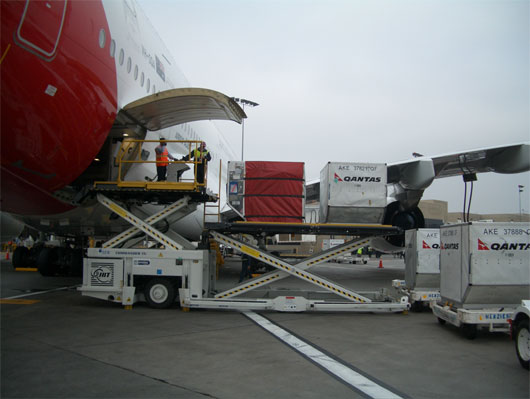
The story behind a story of our time: the HeliRoll.
A quarter of a century ago, the FMC Airline Equipment Division (now known as JBT AeroTech GSE) introduced a revolutionary product that would become one of the greatest success stories in the history of airline ground support equipment. The newly released Commander loader, with its modern, clean looking appearance introduced many new enhancements never seen on cargo loaders, including a swing-out power module, extendable operator cab, powered bridge wings – and something dubbed the HeliRoll conveying system. Looking back, of all of the enhancements, arguably the HeliRoll application had the greatest impact and it helped make the Commander the biggest selling cargo loader around the world.
The HeliRoll conveyor system evolved as the result of customer input that demanded a more reliable and efficient method to move containers and pallets on cargo loaders. Up until 1986, most loaders used rubber belts, rubber wheels and cylinder rollers to convey their loads. For the operators, the current loader conveying systems were slow and laborious and it was not uncommon for containers to be manually jostled on the bridge because of the lack of side shifting features. Maintenance on these systems was costly because the rubber belting would suffer cuts from damaged containers and conveying-lifting systems (which were used to side-shift on the rear platform) becoming damaged through the ingress of foreign matter.
Augurs the answer?
FMC duly formed a cross-functional team, comprising staff from its engineering, sales, field service, purchasing and manufacturing sections, to come up with a new loader to replace the JC/PL-2. One of the key areas that they focused on was how material in other industries was conveyed. The idea of HeliRoll conveying came about after one of the team members described an augur system that they had employed whilst growing up on a farm. The augur idea was transformed into a crude model, which showed a lot of promise during testing.
Tests with the early model revealed was that it was possible to convey product on a flat surface without the use of lifting mechanisms extending and retracting when the need arose to change the product’s direction. The next task was to identify, or design, components that effectively and efficiently conveyed product. Several items were looked at, including an array of omni-rollers and powered wheels. None of these, though, was effective in performing the required functions of container side-shifting and rotation, two key elements in conveying efficiency. The FMC team came to the conclusion that an optimal system was not available – and that it would be up to them to come up with the solution.
Birth of the legend
What the FMC team came up with was the HeliRoll, a unique wheel cluster, or cluster hub, with six freely rotating rollers, positioned at a 45º angle around the hub’s perimeter. When rotated on a shaft, the HeliRoll exerts a force at an angle of 45º to the axis of the shaft. The HeliRoller clusters are either right handed or left handed and work in unison or against each other to move the loads. For example, when conveying a straight load, the HeliRoll clusters move in the same direction, but when side shifting, they work against each other. For rotation, the HeliRoll clusters are mounted in a specific area that allows four opposing forces to create a circular motion. All conveying operations are performed on a single plane, without the need to extend or retract other components. The HeliRoll base and rollers were constructed of aluminum for long life, to be free of rust and to minimize the wear on containers and pallets.
For the end user, the operator, the system was very simple. The loader was divided into three segments, rear-rear platform, front-rear platform and bridge. One joystick in each segment conveyed the load forwards, backwards and sideways. A rotation switch allowed the load on the rear platform to turn. The conveyor system was augmented by cylinder rollers in areas where side-shifting was not necessary. The final outcome was a conveyor system that was fast, easy to control, totally alive and with no dead spots, thereby eliminating the jostling of containers by the operators. JBT declares that the totally live deck is essential when conveying pallets and containers that may have warped or damaged bottoms.
FMC engineers worked with Commander customers in the field, in order to find ways to enhance the Commander’s revolutionary conveying system. In 1990, after extensive field and laboratory testing, the HeliRoll’s rollers were redesigned with new bushings and a curvature design that optimized the movement of the load when it came into contact with the ULD’s surface. With the improved design, the HeliRoll conveyor system has shown itself to be 100% reliable in the worst environmental conditions.
Gilding the lily
Enhancements were also made for maintenance of the conveyor system. The drive chains now have simple adjusters that can be easily accessed and tightened. In the past, when a HeliRoll needed replacement, the platform deck and shaft had to be removed. Today, when replacing a HeliRoll, the damaged cluster is simply cut off and replaced with a two-piece field kit. This task can be performed in less than one hour from under the raised platform with no need to remove the deck plate or shaft.
Dependability is another key element in the design of the system. Should a HeliRoll cluster become damaged, the system keeps on working, without any interruption to the operation. In fact, depending on the location, several clusters could actually be damaged and the system will still operate, with a minimal loss in efficiency.
This conveying system is not just limited to cargo loaders, though. JBT AeroTech has been very successful in selling HeliRoll transfer decks to air cargo facilities around the world. The transfer decks are integrated with the air cargo facilities’ handling systems at transition points and loading areas, or anywhere where the loads must side-shift or rotate. All JBT AeroTech transfer decks require very little maintenance and do not require any embedding into the warehouse floor surface to accommodate mechanical lifting mechanisms.
Other JBT AeroTech products utilizing the HeliRoll include the CLT-8 loader/transporter for side-shifting on the front platform and optional rear container rotation. Moreover, HeliRolls enable the CPT-7ST transporter to efficiently side load, as well as end load and front load ULD containers and pallets.
The popularity and success of the HeliRoll can be measured by the success of the Commander family of loaders, which comprises four models capable of moving loads ranging from 7 tonnes (15,500 pounds) up to 30 tonnes (66,000 pounds). To date, over 5,300 Commanders have been sold worldwide, making it the most popular cargo loader every built. Without doubt the HeliRoll has been a key element that has enabled the Commander to provide a lower cost of total ownership.
In all, JBT AeroTech estimates that over 1.4m HeliRolls have been installed in Commander CLT-8s, CPT-7STs and transfer decks since 1987. That’s a staggering total. Moreover, to date, approximately 56,000 HeliRolls have been sold through JBT AeroTech’s spare parts sales. On that basis, approximately 96% of all the HeliRolls installed are still in use today. In fact, many of the Commander loaders that have been rebuilt actually returned to service with their original HeliRolls intact.
In summary, it is fair to say that JBT AeroTech’s novel system has played a major rôle in the success of the Commander family of loaders and transfer decks. It has eliminated the dead spots on the conveying surface and has given the operator complete control of the load at all times. HeliRolls have proven to be durable and to require little maintenance. Over the years, there have been several attempts by competitors to duplicate this conveyor system, but so far, none has succeeded.
That fact alone says it all.